Glass wool and rock wool are both popular types of insulation materials widely used in the construction and industrial sectors. While they share some similarities in terms of their insulating properties, there are several distinct differences between them in terms of composition, manufacturing process, performance characteristics, and applications.
Composition
Glass wool is primarily made from recycled glass. The production process involves melting the glass at high temperatures, typically around 1500 – 1600°C. Once the glass is in a molten state, it is then spun or blown into fine fibers. These fibers are then bonded together using a binder, usually a thermosetting resin, to form the final insulation product. On the other hand, rock wool is made from natural rocks such as basalt or dolomite. These rocks are melted at extremely high temperatures, often exceeding 1400°C. Similar to glass wool, the molten rock is then processed into fibers, which are also bound together with a binder. The difference in composition gives each material unique properties. For example, the glass – based composition of glass wool gives it a relatively smooth and fine – fiber texture, while the rock – based composition of rock wool results in a more rugged and coarser – fiber structure.
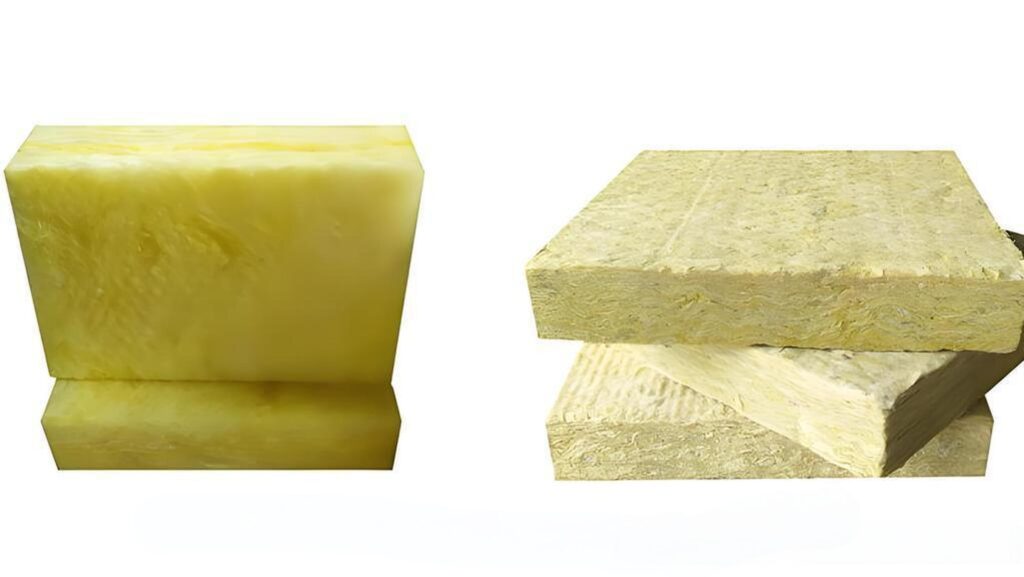
Manufacturing Process
The manufacturing processes of glass wool and rock wool, although both involving fiber – forming from a molten material, have some differences. In the production of glass wool, the molten glass can be spun using a centrifuge – based method. This involves spinning the molten glass at high speeds, causing it to be ejected through small holes and form fine fibers. Another common method is the blowing process, where high – pressure air or steam is used to blow the molten glass into fibers. For rock wool, the molten rock is usually processed through a spinneret – like device. The molten rock is forced through small holes in the spinneret, and as it exits, it is attenuated into fibers by the action of high – velocity air or steam. These differences in the manufacturing process can affect the quality and consistency of the fibers produced, which in turn impacts the performance of the final insulation product.
Performance Characteristics
Thermal Insulation
– Both glass wool and rock wool are good thermal insulators. However, glass wool generally has a slightly lower thermal conductivity value in some cases, which means it can provide better heat resistance under certain conditions. This makes it a popular choice for applications where high – level thermal insulation is required, such as in the insulation of walls and roofs in residential buildings.
– Rock wool, on the other hand, has excellent thermal stability. It can maintain its insulating properties even at high temperatures. This makes it suitable for applications where there may be exposure to heat sources, such as in industrial furnaces or around chimneys.
Acoustic Performance
– Glass wool is known for its good acoustic insulation properties. Its fine – fiber structure is effective in absorbing sound waves, making it a great choice for reducing noise transmission in buildings. It can be used in interior partitions, ceilings, and walls to create a quieter indoor environment.
– Rock wool also has good acoustic absorption capabilities, but its coarser – fiber structure may result in a slightly different sound – absorbing profile compared to glass wool. In some cases, rock wool may be more effective in absorbing lower – frequency sounds.
Fire Resistance
– Rock wool is highly fire – resistant. It has a high melting point due to its rock – based composition and can withstand temperatures of up to 1000°C or more without melting or losing its structural integrity. This makes it an ideal choice for fire – protection applications, such as in fire – rated walls and ceilings in commercial buildings.
– Glass wool is also fire – resistant, but its melting point is generally lower than that of rock wool. It can still provide a certain level of fire protection and is often used in applications where a lower – level of fire resistance is required, such as in some residential insulation projects.
Applications
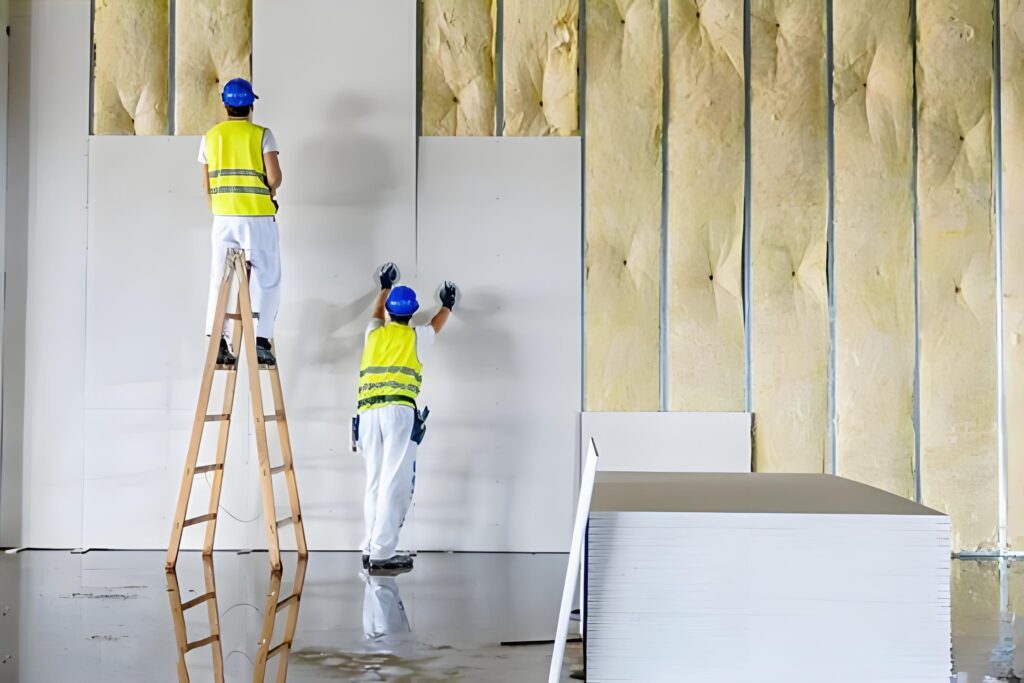
Glass Wool Applications
– In the construction industry, glass wool is commonly used for thermal insulation in walls, roofs, and floors of residential and commercial buildings. Its lightweight nature and good thermal and acoustic insulation properties make it easy to install and effective in creating a comfortable indoor environment. It is also used in HVAC (Heating, Ventilation, and Air – Conditioning) systems for duct insulation to reduce heat loss or gain and to control noise.
– In the industrial sector, glass wool can be found in applications such as insulation of storage tanks, pipes, and equipment where thermal insulation is required.
Rock Wool Applications
– Rock wool is widely used in industrial settings for applications that require high – temperature resistance and fire protection. This includes insulation around industrial furnaces, boilers, and chimneys. In the construction industry, it is used in fire – rated partitions, ceilings, and facades of commercial buildings to meet strict fire – safety regulations. It is also used in some cases for thermal insulation in buildings, especially in areas where there may be a higher risk of fire.
In conclusion, while glass wool and rock wool are both insulation materials with similar functions, their differences in composition, manufacturing process, performance, and applications make them suitable for different scenarios. Understanding these differences can help builders, contractors, and designers make the right choice when selecting insulation materials for their projects.